Technologies
A high willingness to innovate, a healthy dose of good judgment and our uncompromising quality standards have made us one of the leading German manufacturers of printed circuit boards in the sample and small series sector today, with a production volume of up to 100 m² per day. We are ideally equipped to meet even the most demanding requirements for printed circuit boards and multilayers – including yours.
We contribute the following technological expertise to our PCB consulting and production:
- Selection of base material
- Signal integrity testing
- Coatings & Inks
- Stackups / layer stackup
- Drilling & Plating
- Plugging & Filling
- Structures
- Milling/ cutting/ chamfering
- Insulation foil
- Specifications
- Soldering surfaces
- Testing
Every PCB is unique. We work with you to develop the optimum solution and make full use of our broad technological expertise.
Oliver Bertram
Sales Manager
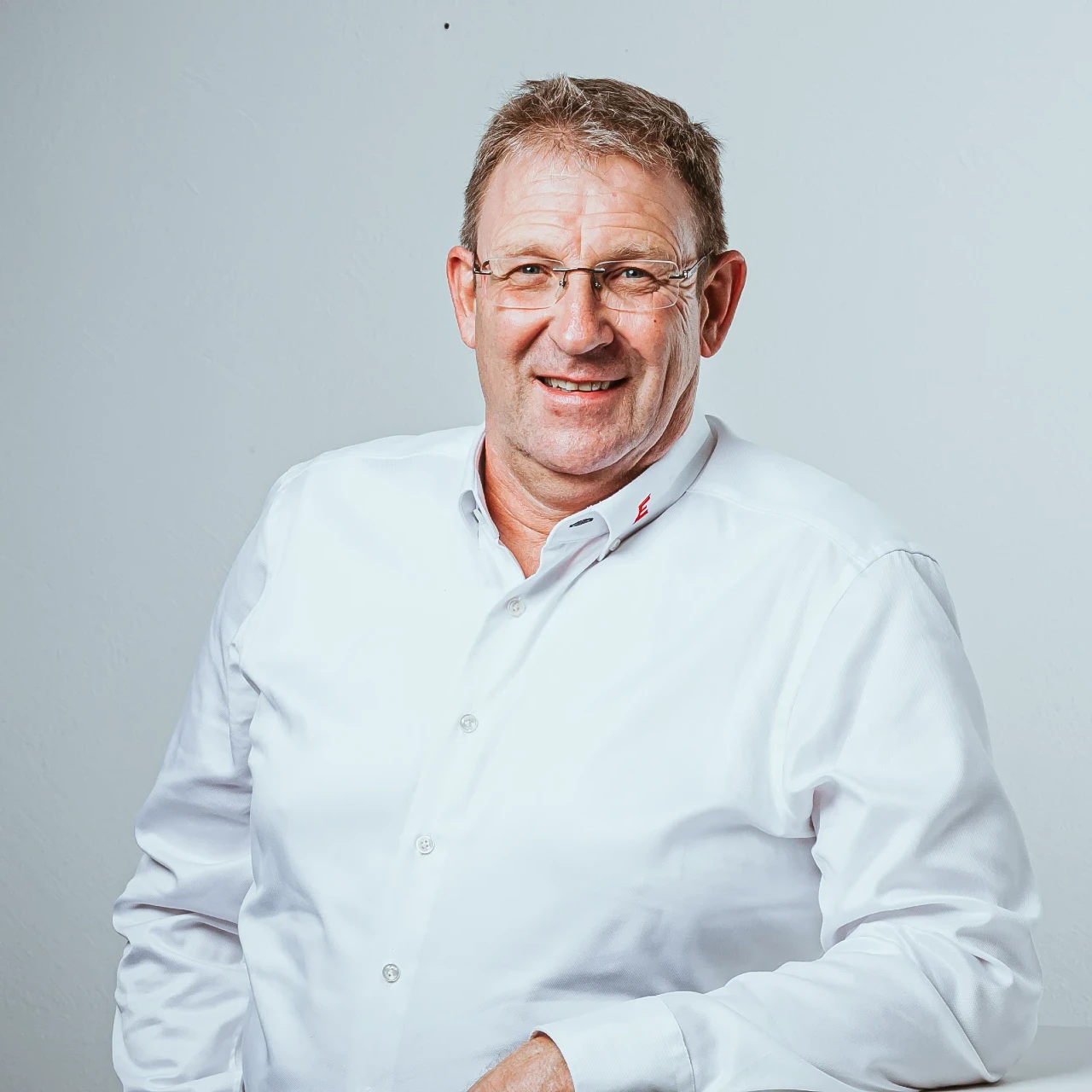